Articles
From Concept to Simulation: Why FEA Engineering Is Critical to Structural Success
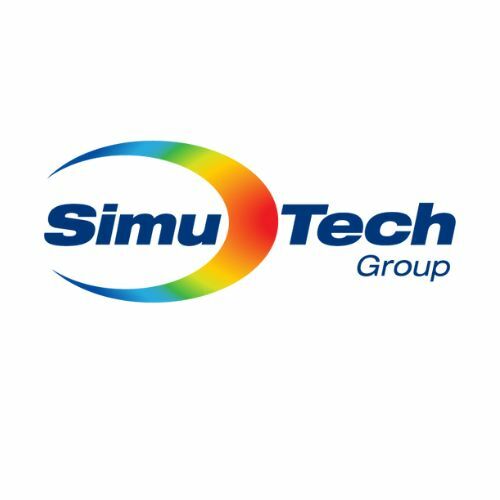
Share article
In today’s fast-paced product development environment, the demand for stronger, lighter, and more efficient structures is higher than ever. Engineers and designers are under constant pressure to deliver innovative solutions that meet both performance and safety standards—without exceeding budgets or deadlines. This is where FEA engineering—short for Finite Element Analysis—plays a pivotal role.
FEA engineering transforms conceptual ideas into validated designs through precise simulations, reducing guesswork and improving structural reliability across industries like aerospace, automotive, civil engineering, and manufacturing.
What is FEA Engineering?
Finite Element Analysis (FEA) is a computational method used to predict how a product or structure will react to real-world forces such as heat, vibration, fluid flow, and other physical effects. It involves breaking down a complex structure into smaller, finite elements, then solving the behavior of each element to predict the overall performance of the design.
Why FEA Engineering Matters in Structural Design?
Structural success doesn’t just depend on aesthetics or functionality—it requires a deep understanding of how materials and geometry behave under various loads and stresses. Traditional methods like hand calculations or simplified models often fall short in evaluating complex structures.
That’s where FEA analysis shines. It enables engineers to perform in-depth Structural Analysis by considering:
Static and dynamic loads
Stress distribution
Deformation patterns
Vibration and resonance issues
These insights allow for better decision-making in material selection, geometry refinement, and manufacturing processes.
From Concept to Simulation: The Workflow
Let’s walk through a typical workflow in FEA engineering, from the initial concept to the simulation phase:
1. Conceptual Design
Every product or structure begins with an idea. At this stage, engineers define design goals, constraints, and functional requirements. The conceptual model may be a rough CAD drawing or sketch. Collaboration with a trusted FEA consulting team can help align initial design choices with simulation-ready geometry.
2. Geometry Preparation
Before the analysis begins, the design is cleaned and simplified to remove unnecessary features (like fillets or holes that don’t impact performance) which could complicate the meshing process. This step is crucial for efficient and accurate FEA analysis.
3. Running the Simulation
Once the model is ready, the FEA solver computes the results. Depending on complexity, simulations can take minutes to hours. The solver calculates displacements, stresses, and strains across the entire model.
The Future of FEA Engineering
With the advancement of AI, machine learning, and cloud computing, the future of FEA engineering is evolving rapidly. AI-assisted meshing, real-time simulation feedback, and integration with generative design are transforming how engineers approach Structural Analysis.
Moreover, as digital twins and Industry 4.0 become more mainstream, FEA will play an even bigger role in real-time performance monitoring and predictive maintenance.
Final Thoughts
From initial concept to final validation, FEA engineering is an indispensable tool in modern structural design. It empowers engineers to explore, test, and optimize designs virtually—saving time, cutting costs, and improving product quality.
In the ever-demanding world of engineering, success isn’t just built—it’s simulated.
Advertisement